Maintenance of your Low-Voltage switchboard: Why and how?
The best way to combat the ageing of equipment while maintaining operation in line with the needs of the installations is to carry out reliable and regular maintenance. The risks associated with poor maintenance of your low-voltage switchboards and systems are often greater than you think.
Why is the maintenance of your Low Voltage switchboard essential?
The 3 issues below are the most common when Low-Voltage switchboard maintenance is not optimal: production stoppage, increasing maintenance costs and unanticipated obsolescence. They represent the risks linked to non-regular maintenance. Knowing them in order to better understand them is part of good equipment management.
The 5 major consequences of a production shutdown
Even if production shutdowns are planned, they remain complex and expensive projects. An unexpected situation can arise at any time and no industry is immune. Planning is impacted and start-up is delayed. An extra day of production stoppage can result in a loss of several million euros.
- Financial losses: Among the companies that have experienced a stoppage of their production line in 2014, more than a quarter of them cite losses of at least €1 million per incident. The biggest losses peak at more than 50 or even 100 million euros per incident.
- Environmental risks: Production shutdown could have a lasting effect on the natural and human environment around the place of production. Its reputation, and therefore its value, may suffer sustainably.
- Industrial consequences linked to processes: Industrial manufacturing processes sometimes require continuous operation and cannot be stopped.
- Need for an Emergency Power System: Power failure of the systems causes urgent need for a back-up system. The search for a service provider and the availability of solutions further lengthens the downtime.
- Layoffs for operational reason: Downtime will obviously have a direct impact on workers who can no longer produce or who are no longer in optimal safety conditions to work.
3 reasons why your switchboard maintenance costs are high
What are we talking about when we talk about maintenance costs? It is the global cost of preventive or corrective maintenance interventions to which we add the cost of maintenance reports, the cost of equipment failures, the cost of maintenance stocks as well as the depreciation of investments in spare parts dedicated to maintenance.
- Poor anticipation of failures: the cost of unanticipated maintenance operations
- Lack of anticipation of the obsolescence of your electrical switchboards: leads to curative maintenance linked to the failure of spare parts
- Lack of an annual maintenance budget: monitor expenses as closely as possible to spread them out over time
Anticipating the obsolescence of your low voltage equipment
Anticipating the obsolescence of your parts protects you from a large number of important risks that including shut down your production. Here is a non-exhaustive list of reasons why it is important to anticipate obsolescence equipment when purchasing a low voltage switchboard.
- Low-voltage installation reliability loss: Parts that reach the end of their life and cannot be replaced weaken your low-voltage switchboard.
- Physical and human risks: If your low-voltage switchboard is less reliable (the equipment no longer fulfils its function), it is also less reliable for your technicians and installations
- Your low-voltage switchboard is no longer upgradeable: If your switchboard or its equipment is obsolete, evolution often becomes impossible
- The cost of your maintenance increases without control: If the equipment becomes obsolete, the stock at the manufacturers will decrease, the parts will become rare and therefore their cost will increase
How can you optimise the maintenance of your electrical installation?
To avoid risks and optimize the maintenance of your Low-Voltage switchboard, simple solutions exist and represent time and financial savings.
5 ways to prevent production shutdown
Consequences of production stoppages for manufacturers have an impact on their productivity and can cause heavy losses. Beyond the financial risk, the inability to deliver quality finished products on time can be problematic and lead to a loss of customer confidence. Some ways to prevent production shutdown:
- Avoid lack of energy with regular maintenance
- Have personnel trained to operate your low-voltage switchboard
- Keep switchboard plans up to date
- Have a maintenance plan
- Anticipate your needs by optimising and modernising your low-voltage installation
6 solutions to explore to reduce your corrective maintenance costs
Corrective maintenance, also called curative maintenance in the case of cause finding, consists in intervening on an installation to repair or change a necessary element for its use. Therefore, corrective maintenance is generally preceded by a breakdown or defect leading to the complete or partial unavailability of the equipment.
- Preventive maintenance as a cost reduction strategy: Preventive maintenance reduces the probability of equipment failure or defect. It helps to reduce costs and improve the safety of your low-voltage installation
- Have a maintenance plan for your infrastructure: Your infrastructure, i.e. your installations and equipment, requires maintenance and therefore the drafting of a conscientious maintenance plan to avoid breakdowns and malfunctions
- Comply with the maintenance standard to preserve your low-voltage installations : Set up by Afnor, the NF X60-000 Avril 2016 standard (former NF X60-010 December 1994, FD X60-000 May 2002) is designed to preserve your low voltage installations, both in terms of equipment value, performance and safety
- Reduce expenses: You benefit from preventive maintenance as part of your maintenance contract and save money
- Ending the "break-repair" cycle: The faster you can fix a technical problem, the lower the repair costs will be. A faulty component can lead to downtime that can be very expensive due to lost productivity for example
- Retrofitting your installations to increase your switchboard's life cycle: This solution makes it possible to replace an obsolete component before it immobilises your system
The 5 maintenance actions to implement to avoid equipment obsolescence
How to avoid obsolescence? When purchasing your electrical switchboard, it is advisable to carefully consider the materials and equipment that make it up. It would be best to choose equipment that is repairable and robust.
For the rest, there are organisational solutions to be considered in order to anticipate the obsolescence of your equipment.
- Keep a technological watch
- Plan gradual replacement of obsolete components
- Keep spare parts in stock
- Modernise its electrical equipment
- The maintenance contract - the complete obsolescence management solution
Why have a maintenance contract with your original manufacturer?
As an original manufacturer of low voltage switchboards, we are able to help you.
Protecting you from production stoppages, a mission for our teams
When an accidental overvoltage, an unexpected mechanical problem or an aggressive environment occurs, defects can cause serious damage and above all a production shutdown. These accidents are often foreseeable and are related to the maintenance of your low voltage installation. Our feedback from thousands of installations enables us to offer you effective solutions to prevent production shutdown.
Regularly scheduled manufacturer's maintenance guarantees to users:
- A decrease in direct costs because there are no additional costs related to the urgency of the intervention
- A decrease in indirect costs due to operational or production shutdown
Above all, it is necessary to anticipate problems that are often known and easy for the manufacturer to anticipate. Thanks to our experience as a manufacturer for more than 80 years, we have defined some essentials concerning the maintenance of our electrical switchboards:
- Visual and functional inspection of the parts and the board
- Cleaning of insulation parts
- Lubrication of mechanical parts
- Write an intervention report with the operating conditions, the recommendations of the parts to be replaced and the next maintenance dates to be planned
To guarantee service level of your installation and reduce your direct costs and risks of production shutdown, we advise you to schedule regular manufacturer maintenance and to subscribe to a maintenance contract that guarantees you:
- assurance of prompt care
- proper management of your maintenance
- preferential and known pricing
Discover our maintenance contract offers
Retrofitting to modernise and maintain your installation
Chez COMECA, nous proposons des solutions de retrofit constructeur « Fabricant d’Origine » lorsque nous travaillons sur nos solutions. Nous sommes aussi capables de vous proposer de la rénovation sur d'autres marques faisant partie de votre parc. Nos solutions de retrofit permettent la rénovation de tiroirs, de disjoncteurs, de relais de protection communicants GemStart version 1 à 4, de cartes de signalisation type MAC, SI, d'automates et d'autres éléments non constructeurs de vos tableaux. En choisissant une solution de retrofit, vous donnez une seconde vie à votre tableau et prolongez la durée de fonctionnement de votre installation électrique.
At COMECA, we offer "Original Equipment Manufacturer" retrofit solutions when we operate on our solutions. We offer you retrofitting other manufacturer brands that are part of your equipment fleet. Our retrofit solutions renovate drawers, circuit breakers, GemStart communicating protection relays version 1 to 4, MAC & SI type signalling cards, PLCs and other non-manufacturer elements of your switchboards.
By choosing a retrofit solution, you give a second life to your switchboard and extend the service life of your electrical installation.
Retrofitting to maintain your installation:
- Circuit breaker retrofit: Our specialists developed retrofit kits to migrate to new generations of circuit breakers by mastering modification studies on your low-voltage switchboards.
- Drawer retrofit: Retrofitting a drawer consists of replacing the old one whose equipment became obsolete. Often we have to change the entire drawer to keep the correct elements arrangement. In this way the drawer is a tested unit that complies with the requirements of the standard.
- Motor protection relay GemStart retrofit: Thanks to our manufacturer know-how we developed a retrofit solution named GemStart5-R allowing you to replace old GemStart version (1, 2, 3 and 4) by the last version GemStart5.
Retrofit for the modernisation of your installation:
- Needle equipment retrofit: Replacing needle-based equipment such as voltmeters and ammeters with a communicating measurement centre
- Obsolete PLC retrofit
Case Study : How did COMECA helped a major actor in the agro-food industry to reduce its maintenance costs?
The main challenges in the maintenance of electrical equipment in the food industry are to guarantee their service continuity as well as their availability. Regular maintenance and anticipation of failures can reduce costs without compromising the safety, reliability or performance of its systems. Aging electrical installations consume more and more energy, have risks of untimely tripping and can cause incidents to property or persons.
The maintenance plan proposed by COMECA SERVICES focuses on 3 challenges:
- The life extension of electrical switchboards aged 50 years, awaiting replacement in 5 to 10 years. Replacing obsolete devices or equipment gives a new lease of life to the switchboard. Their recycling enables the availability of spare parts when needed.
- Reduce failures that lead to plant shutdowns and high curative maintenance costs.
- Increase the available supply in order to reduce downtime. In case of electrical failure, on this type of old switchboards, the fixed part was often damaged. Its restoration required a complete shutdown in order to continue using the equipment. The electrical switchboard is saturated in terms of available space - lack of Unequipped Reserve or reserves (lack of fixed and movable part).
We have responded to these challenges with a two-phase solution:
- An audit of the low-voltage switchboard enabling to detect obsolete, used, or defective parts or equipment, points of attention and switchboard parts that may need to be optimised for better performance.
- A maintenance plan based on the renovation of the equipment in order to, reduce curative maintenance costs, improve safety, increase reliability, extend the life of its installation from 5 to 10 years and replace obsolete or defective equipment (retrofit of 5 Circuit Breakers and revamping of 380 drawers of the TIRATOLE range).
Within our interventions, we advise our customers in order to help them quantify and anticipate their maintenance. Tools and methods such as CMMS computer-aided maintenance management help the maintenance manager to detect areas of progress that will quickly enable him to move towards optimised practices.
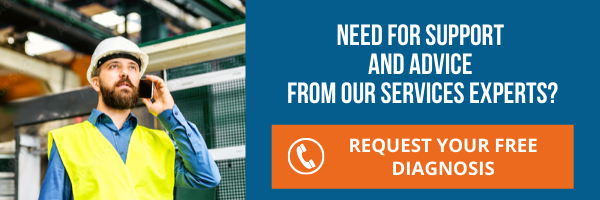